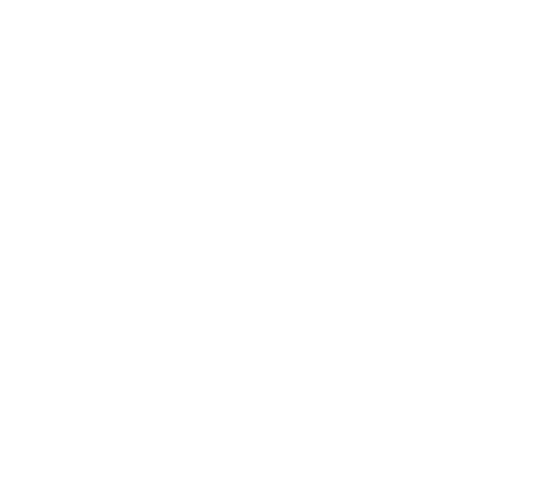
Enhancing Fill-Finish Facility Design with Process Simulation
Process modeling and simulation create a digital representation of real-world systems. With an appropriate model, simulations can be conducted to predict the behavior of a system under various input conditions. There are many types of modeling, including first principles, data-driven models, and models which use elements of both. There are also models centered around scheduling activities and how equipment and resource requirements overlap.
Another type is discrete event simulation. In this case, individual events are tracked, which may require equipment and resources, and may trigger other events. Regardless of the type of simulation used, the goal is to create a simplified abstraction of reality representing the behavior of interest while neglecting, in the interest of efficiency, those aspects of the system which will have a minor effect on the metrics being considered.
Modeling begins with describing the study’s goals, as this will dictate the assumptions, data collection, and complexity of the final model. Metrics will be defined that quantify the approach to the desired goal of the system, usually throughput, cost, and efficiency measures. Once a preliminary model is developed, it must be verified as operating properly and validated against the system being studied. This may be comparing simulation data with real-world data. Or, if that data doesn’t exist, comparing the model results with other similar systems or against the expectations of subject-matter-experts. The base case model is then structured to conduct the study of interest and reach conclusions about how to improve the real-world system.
The primary objective of a fill-finish facility is to efficiently formulate, fill, and package drug products, assuring all safety, efficacy, and purity attributes. Material flow begins at the receiving warehouse. Raw materials (excipient and active pharmaceutical ingredients (API), commodities (vials, cartridges, syringes, stoppers, ampules, or bags), and consumables (filters, single-use systems (SUS), gowning, cleaning supplies, packaging (cartons, inserts, shippers, pallets) are stored and maintained using a computerized enterprise resource planning system (ERP). Schedules are developed to achieve the production plan. This plan includes equipment, facility, material, and personnel requirements. Raw material dispensing, commodity processing, and sterilization are performed in clean preparation areas. The drug product is formulated in bioreactors or tanks and transferred to the filling line through fixed piping or portable tanks. Filling equipment for sterile products may use SUS and ready-to-use (RTU) commodities. The sterile filling machine indexes sterilized commodities to a filling zone where the proper product filling volume is dispensed to the container. The filling machine then places a sterile stopper and seal (vials), or cap (plastic bottles prior to tray loading. Lyophilization, if required, is typically integrated with the filling process. The product at this stage is a work in process (WIP) and returned to the warehouse or transported to the next stage of production. Automated or manual visual inspection and secondary packaging may be in the same or another facility. Quality samples are pulled during appropriate phases of the production process to ensure product specifications are met. Each work center area needs to account for the required throughput, personnel, materials, consumables, testing, storage/staging, waste, cleaning, setup, and utility services.
Each of the elements of a fill-finish line must work together, from dispensing through palletization of the finished product. If any part of the line fails, the entire line will stop. Inputs must be balanced with outputs. Sizing the process for multiple variables (products, equipment, personnel) is complex to plan, particularly with new processes and systems. Do the instantaneous utility needs change or cold storage sizing? There may be minor buffers within the line, only capable of providing or storing material for a very short disruption. Additional staging may be planned between major process steps such as dispensing, formulation, inspection, and packaging. The staging of WIP should be sized to allow for expected disturbances while minimizing its footprint.
This type of manufacturing can be modeled well with a discrete event simulation tool. A typical model here will be built to study equipment utilization, throughput, equipment reliability, and maintenance and to size the staging spaces needed on the line. Product and batch changeovers can be included to understand how they affect throughput; and how reductions in changeover time will increase productivity. Labor can be modeled, providing throughput under various operating schemes and production schedules. Metrics for this type of model are usually overall throughput, equipment utilization, batch cycle time, utility usage vs. time (used to size the utility system), and labor requirements. If equipment reliability is part of the model, then the model can indicate the benefit of reliability improvements (preventive maintenance plans, replacement parts) or projects focused on variability reduction.
The design of a fill-finish facility can be greatly enhanced with process simulation. An appropriate model can identify improvements such as higher throughput and lower cost and indicate where a variability reduction project can have the most impact.